Electrical Rotating Machines Best Practices for Middle East Oil and Gas Industry: Part 2
4. Maintenance Strategy and Planning
A comprehensive maintenance strategy and plan is essential for the reliable operation of electrical rotating machines in the Middle East oil and gas industry. In the industry, where downtime can be costly, a proactive maintenance approach is preferred. Preventive maintenance should be scheduled based on the manufacturer's recommendations, operating hours, and the criticality of the machine. This includes regular inspections of the machine's exterior for signs of damage, loose connections, or leaks. Internal inspections, such as checking the condition of windings, bearings, and commutators (in the case of DC machines), can be done during planned shutdowns at intervals determined by the machine's usage and importance.
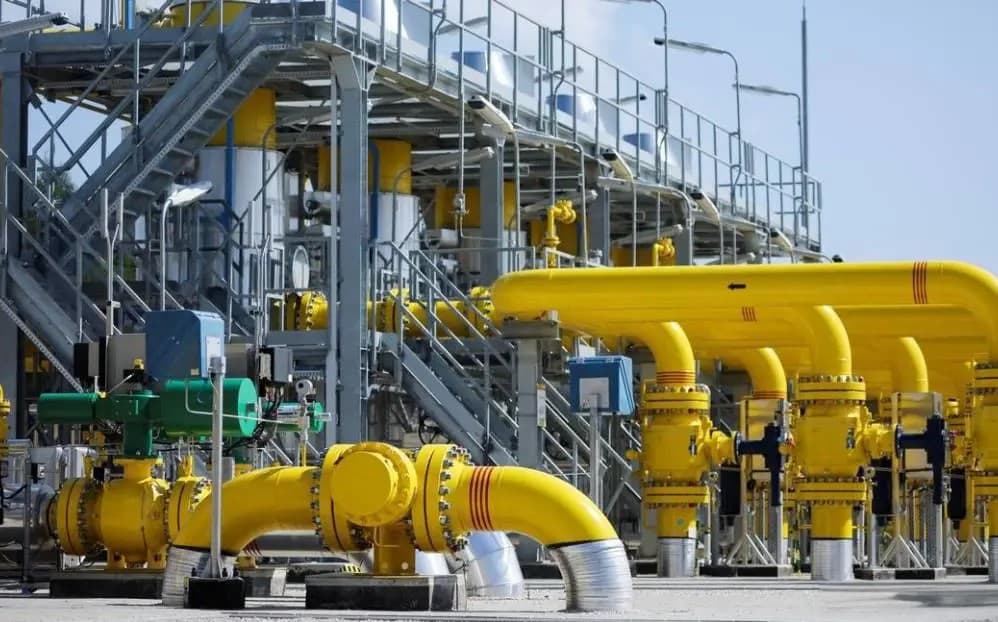
4.1 Condition monitoring and predictive maintenance
Condition-based monitoring (CBM) is a powerful technology that allows operators to assess the health of electrical rotating machines in real-time. CBM, including sensors and monitoring systems, can track parameters such as vibration, temperature, humidity, and electrical characteristics to provide real-time data and information into the operating condition of motors and generators. These data sets can be analysed using advanced analytics and machine learning algorithms to predict when maintenance is needed, allowing for the early detection of issues before they escalate into major failures, as well as for optimise maintenance schedules.
Predictive maintenance, which involves using historical data and advanced analytics, can further enhance the efficiency of CBM. By analysing trends and patterns, operators can predict the remaining useful life of critical components, such as bearings and insulation, and schedule maintenance accordingly. Technologies like vibration analysis, thermography, and oil analysis can provide early warning signs of potential failures. For example, thermography can detect hot spots in the machine that may be caused by overheating due to electrical faults or poor cooling. Using these predictive maintenance tools allows for proactive repairs and replacements, minimising unplanned downtime, extending the operational life of machines and reducing maintenance costs in the long run.
4.2 Vibration monitoring and control
Vibrations are a common issue in rotating machinery, especially in motors and generators. Excessive vibration can lead to damage of critical components such as bearings, shafts, and windings, which can significantly reduce the lifespan of the equipment. In the Middle East oil and gas industry, where equipment operates continuously in harsh environments, vibration monitoring and control are vital to prevent costly downtime.
Modern vibration monitoring systems use sensors that continuously measure vibrations during operation. These sensors, as standard components coming with electrical machines, can detect abnormal vibrations early, allowing for predictive maintenance. By analysing the vibration frequency and amplitude, operators can identify potential issues such as misalignment, unbalanced rotors, or bearing wear. Once identified, corrective actions such as realignment, balancing, or bearing lubrication can be taken before the problem leads to a failure.
4.3 Spare parts management
In the Middle East oil and gas industry, having an efficient spare parts management system for electrical rotating machines is crucial. Given the remote locations of many oil and gas facilities and the potential for long lead times in obtaining parts, maintaining an appropriate inventory of critical spare parts is necessary. This includes items like bearings, seals, brushes (for certain types of machines), and replacement windings. The inventory should be regularly updated based on the usage and failure rates of the parts.
A good spare parts management strategy also involves establishing relationships with reliable suppliers who can provide genuine and high-quality parts in a timely manner. Additionally, parts should be stored in proper conditions to prevent deterioration. For example, bearings and electrical components should be kept in a dry and temperature-controlled environment to maintain their integrity until they are needed for replacement.
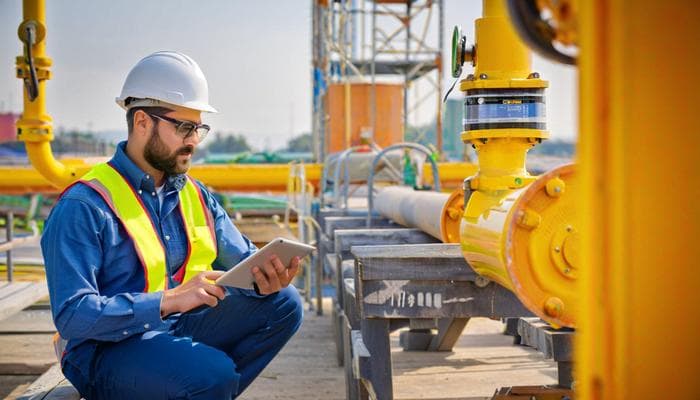
5. Competency, Training and Skill Development
The proper operation and maintenance of electrical rotating machines in the Middle East oil and gas industry rely on the skills and knowledge of the personnel involved. Operators and maintenance technicians should receive comprehensive training and certified to relevant standards on the specific machines they are working with, including understanding the operating principles, installation procedures, and maintenance requirements.
In the industry, where rotating machines operate in some of the most demanding environments, training programs should emphasize not only basic electrical and mechanical skills but also a deep understanding of the specific challenges posed by extreme temperatures, humidity, and corrosive environments.
Working with electrical equipment in an oil and gas environment poses significant risks such as electrical shocks and potential fires due to flammable substances present. Training should cover aspects like safety protocols in the hazardous area to avoid accidents during installation, operation, and maintenance procedures. Training should also cover advanced topics such as vibration analysis, condition monitoring techniques, and the use of predictive maintenance tools. Special training programs for troubleshooting and repair, combined with on-the-job training, can significantly improve the operational efficiency and safety of rotating machines.
Regular refresher courses and training on new technologies and maintenance techniques should also be provided to keep the personnel updated. For example, as new types of motors with advanced control systems or generators with improved efficiency features are introduced in the industry, the workforce needs to be trained to operate and maintain them effectively. Competency assessments can be conducted periodically to ensure that the personnel are capable of performing their tasks to the required standards.
6. Technology and Innovations
Advances in technology are playing a significant role in improving the selection, installation, and maintenance of electrical rotating machines in the oil and gas industry. The integration of electrical rotating machines with other industrial systems, such as enabled sensors, automation and control systems, will be more popular to increase operation reliability. Industrial Internet of Things (IIoT)-enabled sensors can transmit data from motors and generators directly to a central system, where it can be analysed to detect any performance deviations. The use of IIoT can also enhance safety by providing early warnings of potential issues and enabling remote control of the machines. This integration can enhance overall operational efficiency, enabling more precise control and optimisation of industrial processes.
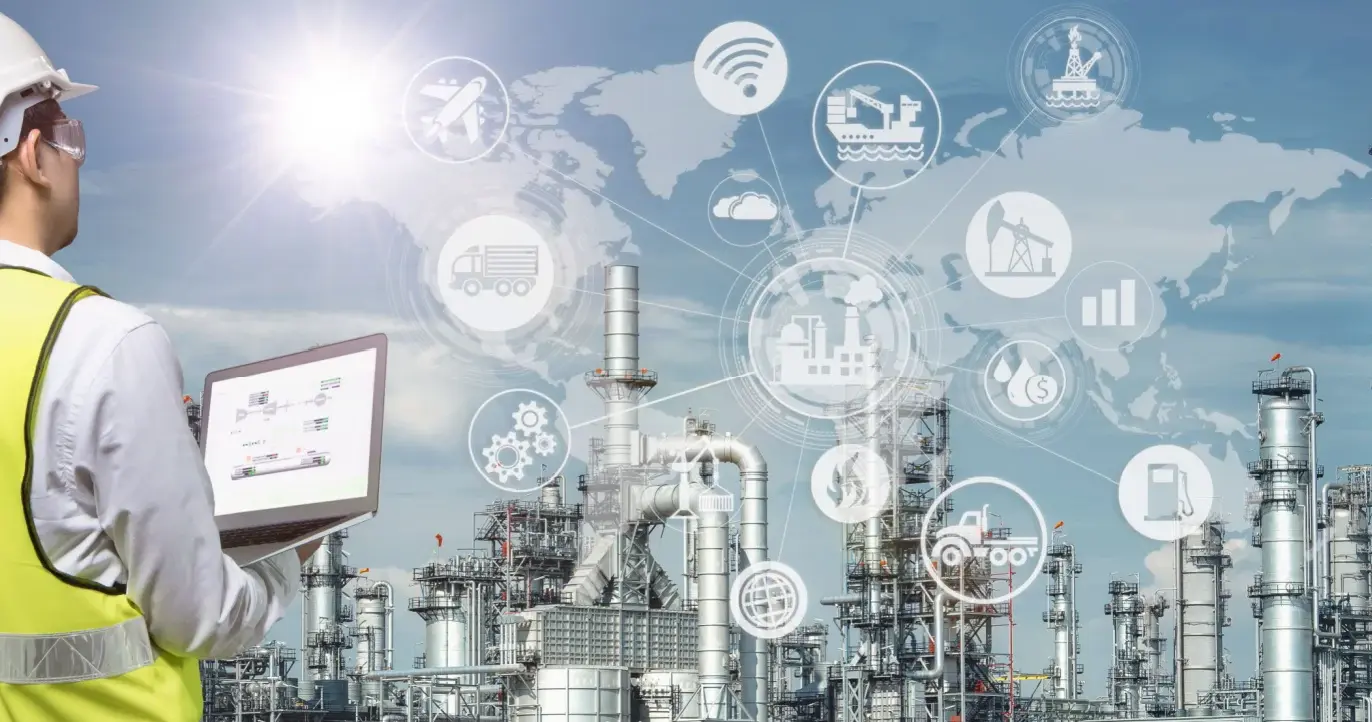
The use of digital twins, for example, allows for the creation of virtual replicas of the machines, enabling simulations and predictive analytics. This can help in optimising machine design, improving installation practices, and enhancing maintenance strategies. The further use of digital twins with this automation integration can provide a comprehensive view of the entire industrial ecosystem.
Artificial intelligence (AI) and machine learning (ML) are other technologies that are revolutionising the maintenance of electrical rotating machines. By analysing historical data and real-time data from the machines, AI and ML algorithms can predict failures, optimise maintenance schedules, and improve overall machine performance. These technologies enable operators to move from traditional reactive maintenance to a more proactive approach, reducing operational risks and improving machine reliability. They can also help in identifying the root causes of failures, enabling more effective troubleshooting and repair.
The electrical connections must be made accurately and in accordance with the manufacturers’ specifications and relevant electrical installation codes and standards. High quality cables with appropriate insulation and current-carrying capacity should be used. In areas prone to corrosion due to humidity or exposure to chemicals in the oil and gas environment, the connectors and terminals should be protected with corrosion-resistant coatings or sealed properly. Additionally, proper grounding of the machines is crucial to ensure electrical safety and to protect against electrical faults and lightning strikes. Grounding systems should be regularly inspected and maintained to maintain their integrity.
The increasing focus on sustainability and energy efficiency will drive the adoption of high-efficiency motors and generators, as well as the use of renewable energy sources. Advances in technology, such as AI, ML, and IIoT, will continue to enhance the selection, installation, and maintenance of these machines, improving reliability and reducing downtime.
7. Conclusion
The Middle East oil and gas industry depends on electrical rotating machines for its core operations, and ensuring their proper selection, installation, and maintenance is essential for its continued success. A holistic approach that encompasses all these best practices is necessary to overcome the challenges posed by the unique operating environment of the Middle East oil and gas industry, and to optimise the utilisation of electrical rotating machines for the benefit of the sector and the region's energy infrastructure as a whole. As the industry continues to embrace new technologies and digital solutions, the future of electric rotating machines business in the Middle East oil and gas sector looks brighter, more reliable, and more cost-effective.
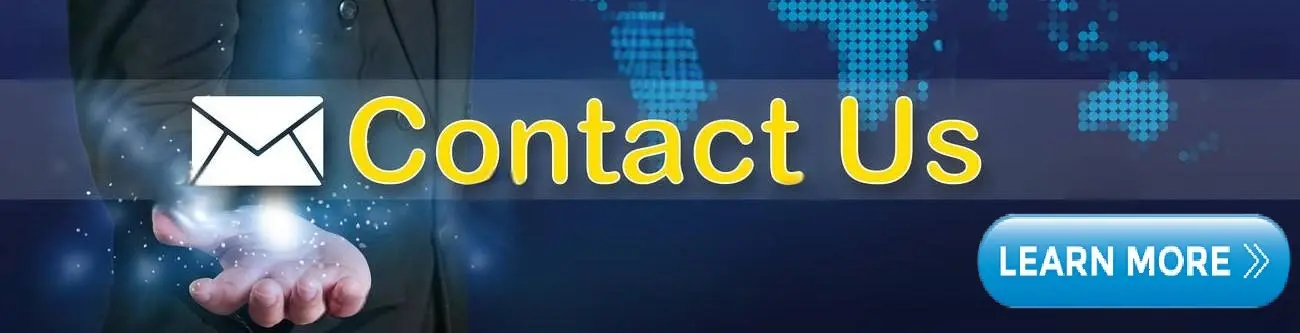
Back