Electrical Rotating Machines Best Practices for Middle East Oil and Gas Industry: Part 1
1. Introduction
The Middle East oil and gas industry is a critical sector that relies heavily on electrical machines such as motors and generators. These rotating machines play a vital role in powering various processes, from drilling operations to pumping and refining activities that facilitate extraction, processing, and transportation of oil and gas. Ensuring their proper selection, installation, maintenance, and personnel training is of utmost importance to guarantee continuous and efficient operation in the often harsh and demanding environments of the region. The unique climatic conditions, including high temperatures, sandstorms, and humidity in some areas, along with the need for high reliability due to the nature of oil and gas operations, pose significant challenges. This article will explore the best practices, know-how and technologies associated with these aspects to optimise the performance and lifespan of electrical rotating machines in the Middle East oil and gas industry.
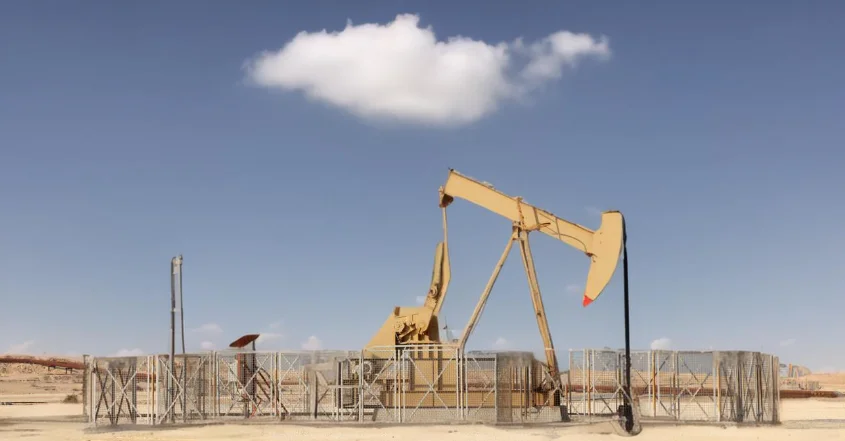
2. Selection of Electrical Rotating Machines
2.1 Machine types
The selection of electrical rotating machines for the oil and gas industry involves careful consideration of several factors, including the specific application, environmental conditions, and operational requirements. In the Middle East, where extreme temperatures and harsh desert conditions are common, selecting machines that can withstand these challenges is paramount. High-temperature ratings, dust-proof enclosures, and corrosion-resistant materials are essential features to look for. Additionally, the machines should be designed to handle the specific loads and operational cycles of the oil and gas processes on platforms with sufficient foundation stiffness.
One of the key considerations in selecting electrical rotating machines is energy efficiency. With the increasing focus on sustainability and cost reduction, high efficiency class motors and generators are preferred. These machines not only reduce energy consumption but also lower operational costs and carbon emissions. The use of variable frequency drives (VFDs) can further enhance energy efficiency by allowing for precise control of motor speed and torque, matching the machine's output to the actual load requirements.
Another critical aspect is the selection of the appropriate type of motor or generator based on factors including the required power rating, speed, voltage, and type of load the machine will drive. For motors, the choice between induction motors, synchronous motors, and DC motors depends on the application. Induction motors are commonly used due to their robustness and reliability, while synchronous motors are preferred for applications requiring precise speed control and power factor correction. For generators, the choice between diesel, gas, or electric driven units depends on the available fuel sources and the specific power requirements. In offshore applications, submersible motors designed to operate underwater are essential.
2.2 Environmental conditions
In addition to power requirements, the protection features of the motor or generator must be carefully chosen for oil and gas industry. Due to the nature of the business, explosion-proof and flameproof motors are essential for hazardous locations such as oil rigs and gas processing plants. These motors are designed to prevent ignition of explosive gases or dust particles in the surrounding atmosphere.
The high ambient temperatures in the Middle East can impact the performance and cooling needs of the machines. Motors and generators should be selected with appropriate insulation classes that can withstand these elevated temperatures. For instance, machines with Class F or Class H insulation are often preferred as they can handle higher temperature ranges compared to lower-class insulations. Motors with built-in cooling systems, such as air or water-cooled types, help manage the heat produced during operation, ensuring the motor does not overheat. Additionally, protection against dust and sand ingress is essential, given the prevalence of sandstorms. Machines with sealed enclosures or effective filtering systems to prevent particulate matter from entering and causing abrasion or short circuits are more suitable.
Corrosion is one of the leading causes of failure for electrical rotating machines in the Middle East’s harsh environments. Saltwater exposure, high humidity, and aggressive chemicals from the oil and gas process can accelerate the degradation of metal components. As such, selecting motors and generators with special paint coating or corrosion-resistant materials is vital.
2.3 Compatibility with the power grid
In the Middle East oil and gas industry, electrical rotating machines need to be compatible with the local power grid. The grid characteristics, such as voltage levels (which can vary from country to country or even within different regions), frequency (usually 50 Hz or 60 Hz), and power quality, influence the selection. For example, if a generator is being installed to supply power during grid outages or as part of a distributed generation system, it must be able to synchronise properly with the grid when it comes back online. Motors also need to operate smoothly within the voltage and frequency variations that may occur on the grid. Some modern motors are equipped with variable frequency drives (VFDs) that can adjust the speed and power consumption based on the grid conditions, improving energy efficiency and reducing stress on the machine during fluctuations.
Moreover, harmonic distortion is a concern in many industrial power systems. Selecting motors and generators that are less sensitive to harmonic currents and, if necessary, implementing harmonic filters can prevent overheating and premature failures caused by distorted waveforms. This is especially important in facilities with a large number of nonlinear loads like variable speed drives and power electronics-based equipment commonly found in oil and gas processing plants.
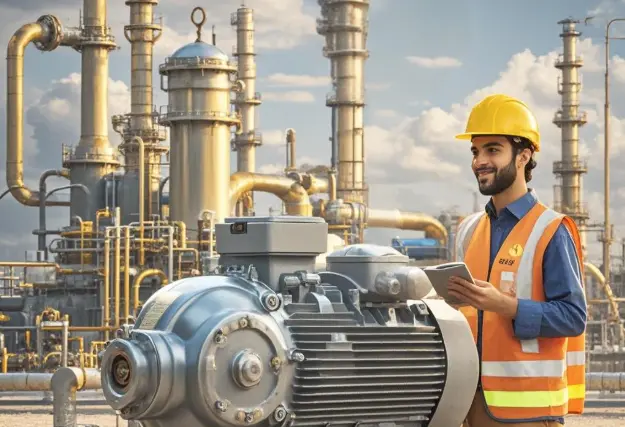
3. Installation Best Practices
3.1 Foundation
Proper installation of electrical rotating machines is essential for their long-term performance. Incorrect installation can lead to premature wear, overheating, or even catastrophic failures. The installation site should be carefully prepared, ensuring that the foundation is stable and level to prevent vibrations and misalignment. In the Middle East, where the soil conditions can vary, proper engineering of the foundation to account for factors like soil settlement and seismic activity (in some regions) is necessary. For large generators or motors, a vibration isolation system may also be installed to further reduce any transmission of vibrations to the surrounding structure and to protect the machine itself from external vibrations.
3.2 Alignment and coupling
Correct alignment between the rotating shafts of motors and the driven equipment (such as pumps, compressors, etc.) is vital. Misalignment can lead to excessive vibrations, premature wear of bearings, shaft damage, and reduced efficiency. In the oil and gas industry, where precision in operation is key, laser alignment tools are commonly used to achieve precise alignment, ensuring that the shafts of the motor and the driven equipment are perfectly aligned. This not only extends the lifespan of the machine, but also reduces the risk of failures and downtime.
Couplings between the motor and the driven component should also be selected carefully. Flexible couplings are commonly used as they can accommodate small misalignments and reduce the transmission of shock loads, which can be beneficial in applications where there may be variations in operating conditions or startup/shutdown cycles.
During installation, the coupling should be properly installed and tightened according to the manufacturer's guidelines. Regular checks of the alignment and coupling condition should be part of the maintenance routine to detect any changes that could affect the performance of the rotating machine and the connected equipment.
3.3 Electrical connections
The electrical connections must be made accurately and in accordance with the manufacturers’ specifications and relevant electrical installation codes and standards. High quality cables with appropriate insulation and current-carrying capacity should be used. In areas prone to corrosion due to humidity or exposure to chemicals in the oil and gas environment, the connectors and terminals should be protected with corrosion-resistant coatings or sealed properly. Additionally, proper grounding of the machines is crucial to ensure electrical safety and to protect against electrical faults and lightning strikes. Grounding systems should be regularly inspected and maintained to maintain their integrity.
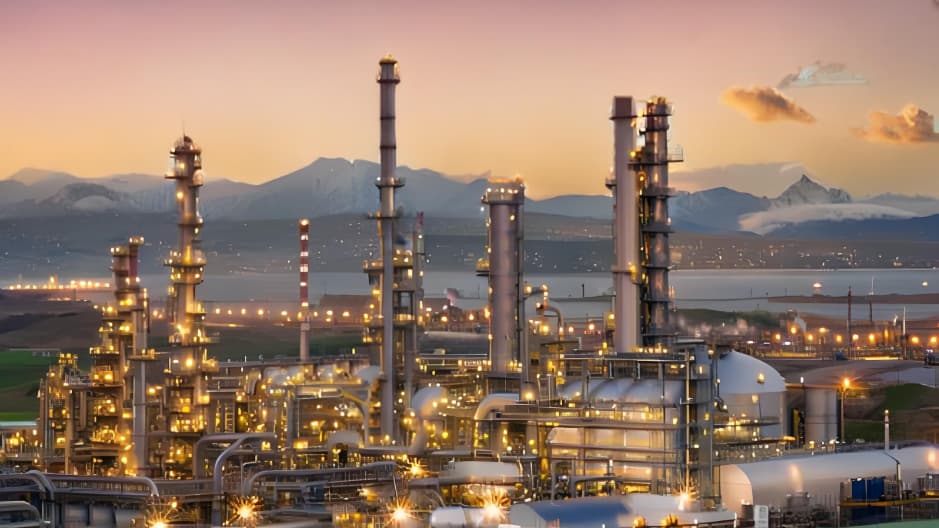
3.4 Lubrication and cooling
Effective lubrication is essential for the smooth operation of motors and generators, reducing friction and wear between moving parts, particularly bearings. Given the high temperatures in the Middle East, proper lubrication and cooling of electrical rotating machines are critical. The lubricating oil or grease used in bearings and other moving parts should have suitable viscosity and thermal stability properties to function effectively under elevated temperatures. High quality synthetic lubricants are often recommended as they can withstand the harsh conditions and provide better protection against wear and friction.
Automated lubrication systems can deliver the precise amount of lubricant at the right time, reducing the risk of over-lubrication or under-lubrication. These systems also eliminate human error and reduce maintenance intervals. In offshore applications or remote locations, the use of synthetic lubricants can offer superior performance due to their higher resistance to temperature extremes and longer service life. Regular oil analysis should be conducted to monitor the condition of the lubricant, checking for contamination, degradation, and wear particles. Based on the analysis results, timely oil changes or lubricant top-ups can be carried out.
Cooling systems are another important consideration during installation. In the hot and arid conditions of the Middle East, effective cooling is essential to prevent overheating and ensure optimal performance. Air-cooled machines should have adequate ventilation paths that are kept clear of dust and debris. In some cases, additional cooling fans or heat exchangers may be installed to enhance the cooling capacity. For water-cooled systems, which are sometimes used for larger machines or in applications where more efficient cooling is required, the quality of the cooling water must be monitored regularly. Water treatment processes may be necessary to prevent scale formation, corrosion, and biological growth that could clog the cooling channels and reduce the cooling efficiency.
Last but not least, the proper handling of machines during installation is critical to prevent damage. Large motors and generators should be transported carefully to avoid mechanical stresses on sensitive components. Protective covers should be used during the installation process to shield the equipment from dust, moisture, and other contaminants. Adequate ventilation systems must also be installed to prevent overheating, particularly in environments where ambient temperatures are high.
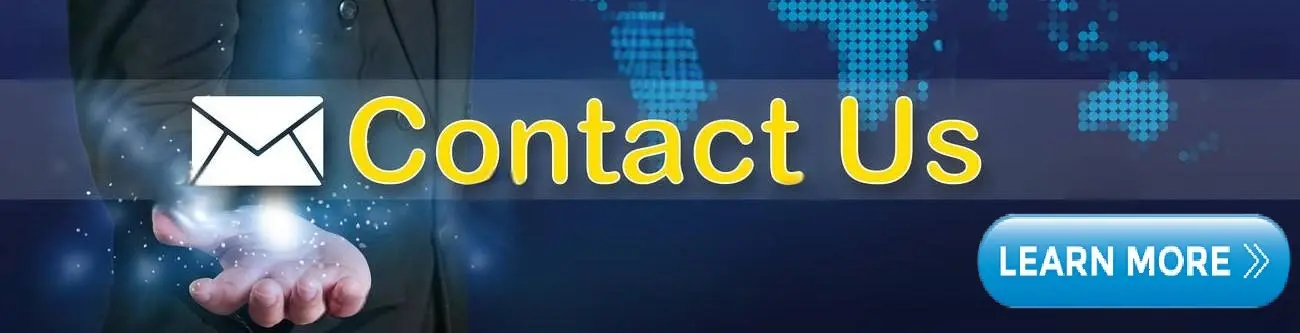