Finite Element Analysis for Industrial Challenges
Introduction to Finite Element Analysis
Finite Element Analysis (FEA) is a computational technique used to predict how products and systems behave under real-world conditions, such as forces, heat, vibrations, and fluid flow. By breaking down complex structures into smaller, manageable elements, FEA simulates performance and identifies potential weaknesses or optimisations. This method is indispensable for engineering industries, enabling cost-effective, safe, and innovative designs while reducing physical prototyping and testing.
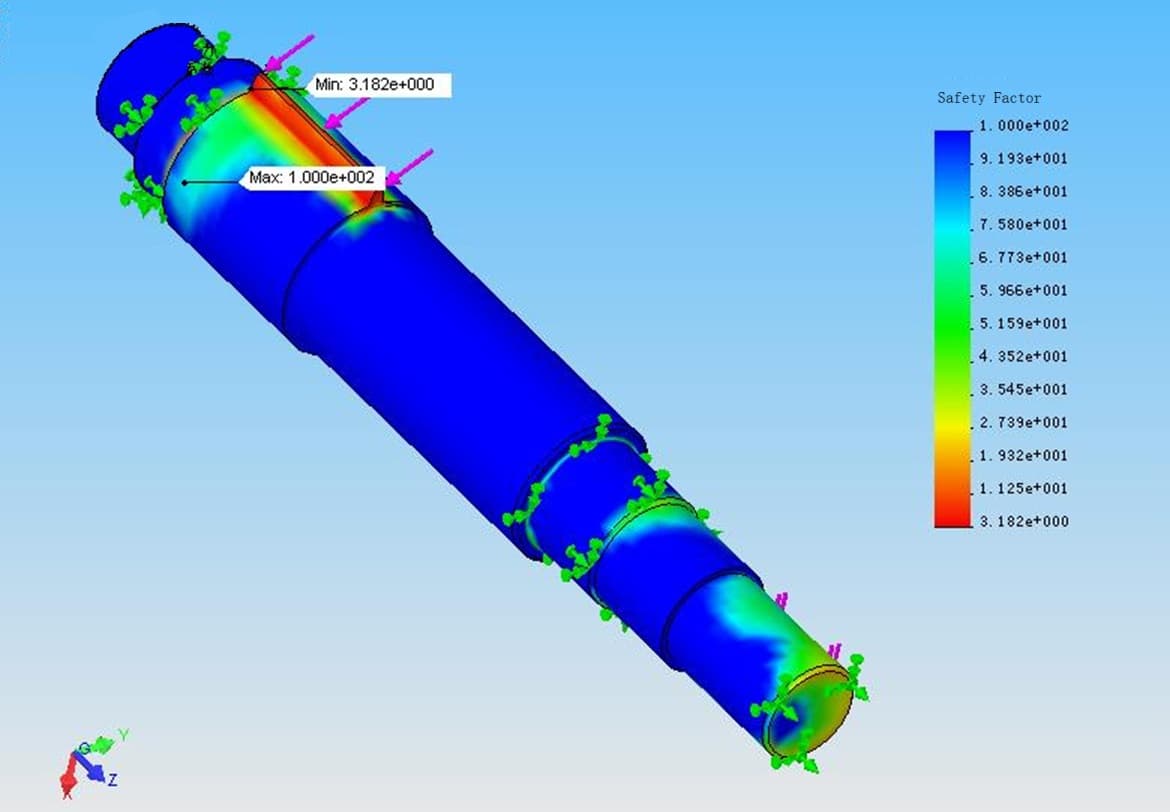
Our Core Capabilities
1. Stress & Structural Analysis
We evaluate how components and systems withstand mechanical loads, ensuring safety, longevity, and compliance with international standards.
- Applications: For example, pressure vessels, pipelines, and storage tanks in petrochemical plants. Wind turbine foundations, offshore platform jackets, and marine hulls. Nuclear reactor containment structures and seismic supports.
- Methodologies: Static and dynamic load simulations (e.g., wind, wave, and gravity forces). Fatigue and fracture mechanics to predict lifecycle performance. Buckling analysis for slender structures like towers and risers.
- Deliverables: Stress contour plots, safety factor reports, and failure risk assessments, etc.
2. Vibration & Shock Analysis
We simulate dynamic environments to ensure systems withstand transient forces, resonance, and sudden impacts.
- Applications: For example, seismic qualification of nuclear power plant components. Vibration damping for offshore wind turbine nacelles. Shock resistance of marine equipment during collisions or explosive events.
- Methodologies: Modal analysis to identify natural frequencies and avoid resonance. Transient dynamics for impulse responses (e.g., wave slamming, machinery startups). Random vibration analysis for equipment in turbulent environments.
- Deliverables: Frequency response spectra, displacement-time histories, and damping optimisation strategies, etc.
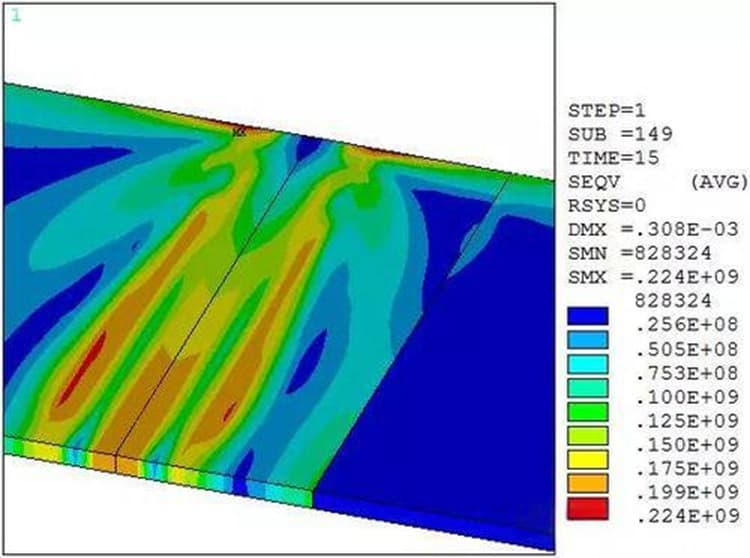
3. Non-Linear Analysis
We simulate dynamic environments to ensure systems withstand transient forces, resonance, and sudden impacts.
- Applications: For example, seismic qualification of nuclear power plant components. Vibration damping for offshore wind turbine nacelles. Shock resistance of marine equipment during collisions or explosive events.
- Methodologies: Modal analysis to identify natural frequencies and avoid resonance. Transient dynamics for impulse responses (e.g., wave slamming, machinery startups). Random vibration analysis for equipment in turbulent environments.
- Deliverables: Frequency response spectra, displacement-time histories, and damping optimization strategies, etc.
4. Thermal Analysis
We specialise in predicting thermal performance and mitigating risks from heat transfer, thermal expansion, and energy dissipation.
- Applications: For example, nuclear fuel rod thermal-structural coupling during operation. Heat exchanger efficiency in petrochemical refineries. Solar thermal receiver components exposed to concentrated solar flux. Battery thermal management in renewable energy storage systems.
- Methodologies: Steady-State & Transient Analysis: Steady-state for equilibrium temperatures; transient for time-dependent thermal cycling (e.g., startup/shutdown). Conjugate Heat Transfer (CHT): Combined fluid flow and solid heat transfer (e.g., cooling systems for marine engines). Thermo-Structural Coupling: Stress analysis due to thermal expansion/contraction (e.g., pipeline hot spots). Thermal Fatigue: Predicting crack initiation from cyclic thermal loads.
- Deliverables: Temperature distribution maps, heat flux vectors, and recommendations for insulation/refractory materials.
Industry-Specific Expertise
Below is a detailed breakdown of how we apply FEA to address unique challenges and deliver value across key industries.
- Renewable Energy: Designing sustainable energy systems requires balancing efficiency, durability, and environmental resilience. Cyclic loading (wind/tidal forces), composite material behavior, fatigue in harsh climates.
- Oil & Gas: Equipment must endure extreme pressures, corrosive environments, and subsea conditions while minimising downtime. Stress corrosion cracking (SCC), thermal cycling in pipelines, buckling in deepwater risers.
- Petrochemical: High-temperature reactors, cryogenic storage, and aggressive chemical exposure demand robust material and design solutions. Creep in furnace tubes, thermal shock in catalysts, flange leakage under thermal gradients.
- Nuclear: Safety-critical components require fail-safe designs under radiation, thermal spikes, and seismic events. Irradiation-induced embrittlement, thermal fatigue in reactor coolant systems.
- Marine & Offshore: Structures must survive corrosive seawater, hydrodynamic loads, and accidental impacts. Slamming loads on ship hulls, vortex-induced vibration (VIV) in risers, ice-structure interaction.
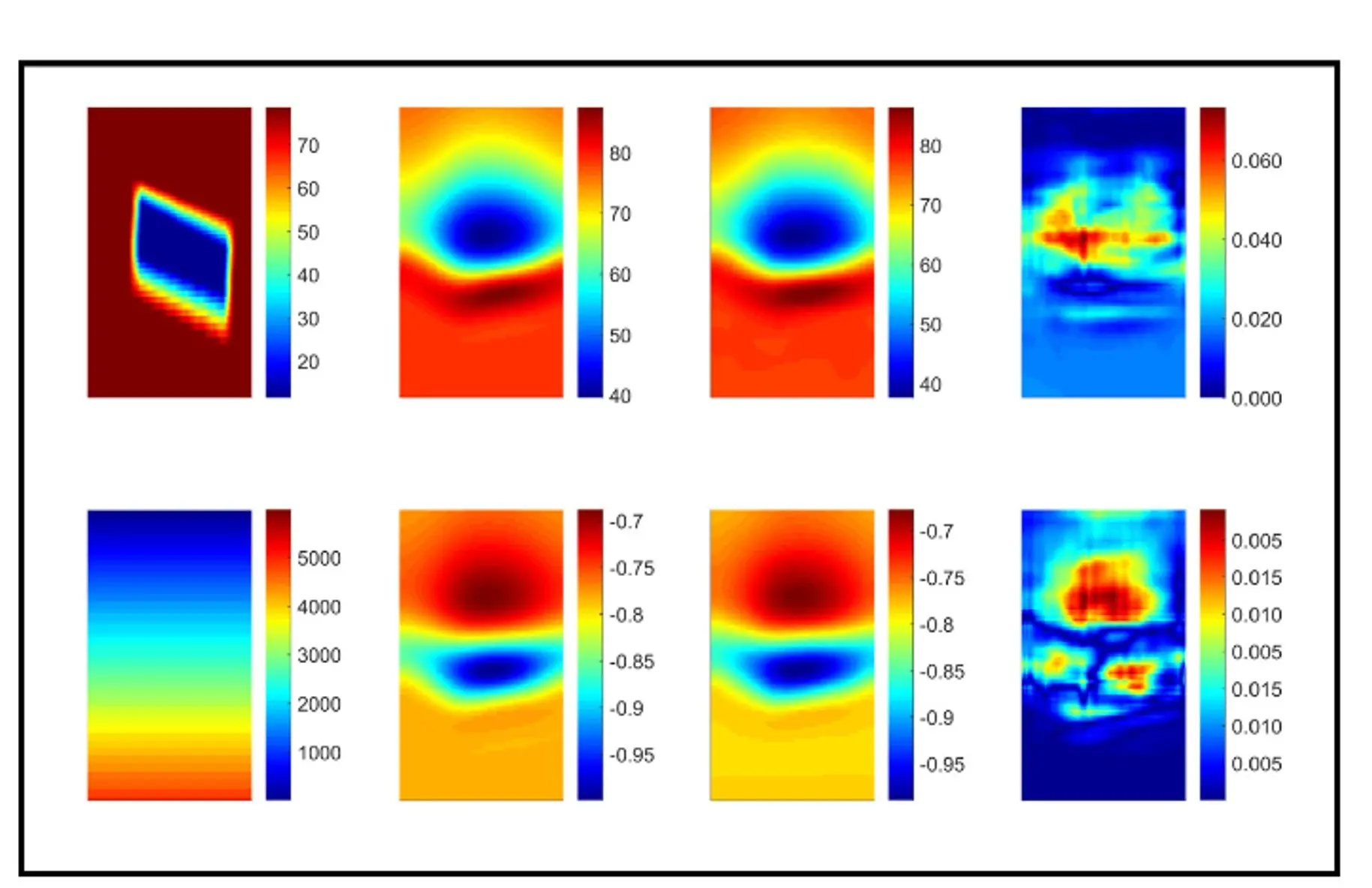
Why Choose Us?
Our multidisciplinary approach combines these capabilities to solve multiphysics challenges. By integrating these analyses, we deliver holistic insights that drive innovation, safety, and efficiency across industries. Here are some examples:
- Proven Experience: Decades of FEA projects across high-risk, safety critical industries.
- Tailored Solutions: From concept validation to failure investigation and regulatory compliance.
- Regulatory Mastery: Familiarity with DNV, ASME, API, IAEA, and Lloyd’s Register, RCC-M standards.
Get in Touch
Looking for accurate and efficient finite element analysis (FEA) services? Our FEA analysis service delivers top-notch results to optimise your design process. Contact us today at inforotextechnologies.com for a free consultation and take your engineering projects to the next level!