Production Challenges of Silicon Anode Battery Technology
1. Introduction
The development of silicon anodes for lithium-ion batteries has garnered significant attention due to their potential to enhance energy density, improve cycle life, and reduce costs. Silicon has a theoretical capacity of about 4200 mAh/g, which is approximately ten times higher than that of traditional graphite anodes. This makes them an ideal component for next-generation batteries, particularly for electric vehicles (EVs) and renewable energy storage systems. However, the production of silicon anodes presents several challenges, particularly in terms of scaling up the manufacturing process. We provide an in-depth analysis of the silicon anode production process, key equipment, challenges for scaling up, and the impact of electrochemistry, think film and plasma coating technologies on the production process.
2. Silicon Anode Production Process
The production of silicon anodes involves several stages, from the sourcing and processing of silicon to the final preparation of the anode material. The process includes the following production stages.
2.1 Silicon Sourcing and Refining:
The production of silicon anodes begins with the preparation of raw materials. The first step in silicon anode production is sourcing high-purity silicon. Silicon is typically derived from silicon dioxide (SiO2) found in sand or quartz. The purification process involves chemical refining to remove impurities such as iron, aluminium, and calcium. It undergoes a reduction process at high temperatures using carbon to form silicon metal. This silicon metal is then refined to obtain the necessary purity for battery applications. For battery-grade silicon, the material needs to be purified to levels of over 99.9%, often through chemical processes like the Siemens process or other advanced refining methods.
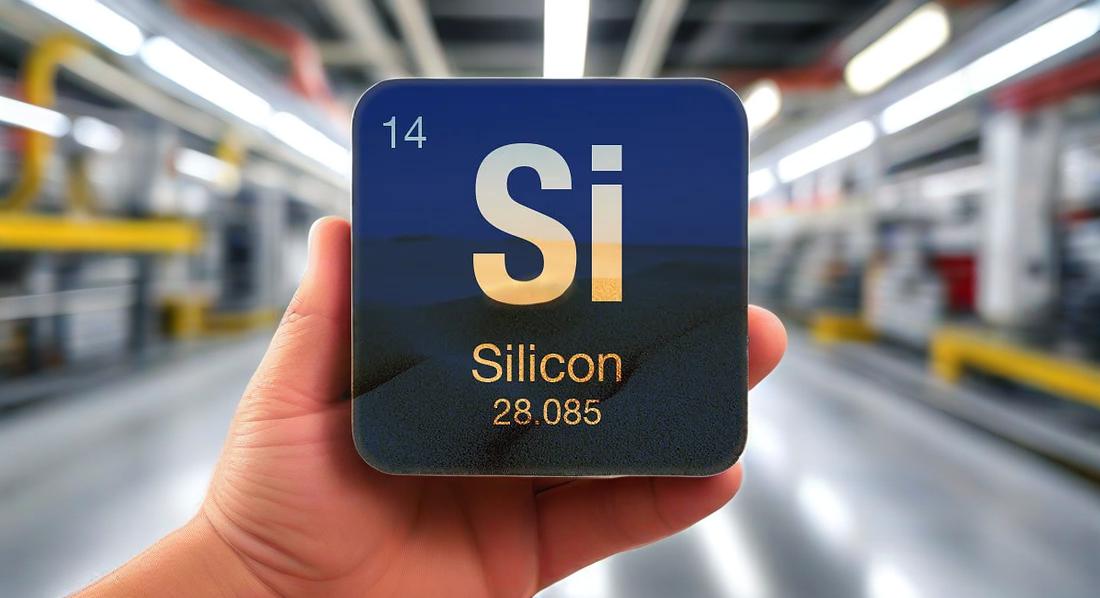
2.2 Silicon Nanostructure Formation:
Silicon anodes generally consist of silicon in the form of nanoparticles, nanowires, or nanosheets. These nanostructures are designed to mitigate the volumetric expansion and contraction of silicon during charging and discharging cycles. Various synthesis methods are employed to create these nanostructures, including
- Chemical vapour deposition (CVD): Gas-phase synthesis of silicon nanoparticles, in most cases plasma enhanced PECVD method uses the chemical reactions of gases that are introduced into a vacuum chamber for producing thin, high-quality films for battery applications;
- Laser ablation: High-energy laser beams decompose silicon-containing gases into nanoparticles; and
- Ball milling: Mechanical grinding of bulk silicon into nanoparticles. It is commonly used to break down bulk silicon into fine particles or powders that can be used to form the anode.
2.3 Silicon Composite Formation:
To overcome the inherent challenges of silicon, such as poor conductivity and significant expansion during cycling, silicon is typically combined with other materials such as graphite, carbon, or conductive polymers. This composite helps maintain the structural integrity and conductivity of the anode. Silicon nanoparticles are mixed with conductive additives (e.g., carbon black) and binders (e.g., polyacrylic acid or carboxymethyl cellulose) to form a slurry. The slurry is then coated onto a copper foil current collector using a slot-die or doctor blade coating process
2.4 Coating and Drying:
The slurry containing the silicon composite is coated onto a thin copper foil, which acts as the current collector. This process is performed using a doctor blade, slot die coating, or spray coating method. After coating, the electrodes undergo a drying process to remove any solvents and ensure the slurry adheres properly to the copper foil, followed by calendering to achieve the desired thickness and density.
2.5 Electrode Formation:
The dried electrodes are then cut to the desired size and undergo a series of pressing steps to ensure the uniformity of the electrode thickness and improve the mechanical integrity of the structure. The electrodes are then assembled into battery cells, where they are paired with a cathode, electrolyte, and separator to form a full battery.
2.6 Electrochemical Testing:
The assembled cells undergo rigorous testing to evaluate performance metrics such as capacity, cycle life, and rate capability.
3. Key Equipment in Silicon Anode Production
The production of silicon anodes requires specialised equipment at each stage of the manufacturing process. Some of the critical equipment used includes:
- Ball Mills: Ball mills are essential for breaking down large pieces of silicon into finer particles for use in anodes. This milling process helps achieve the desired particle size and uniformity necessary for optimal performance in batteries.
- Plasma-Enhanced Chemical Vapour Deposition (PECVD) Reactors: The PECVD reactor is the central piece of equipment used to produce thin films of silicon or silicon-based materials, such as silicon carbide or silicon oxide. It is typically made of stainless steel and is designed to house the vacuum environment in which the deposition occurs. The reactor is equipped with electrodes for creating plasma and an inlet system for introducing precursor gases.
- Coating Machines: Coating machines, including doctor blades and slot die coaters, are used to apply the silicon slurry to the copper foil. These machines ensure that the coating is uniform and adheres properly to the current collector.
- Drying Ovens: After the coating process, drying ovens are used to remove the solvents from the slurry, ensuring the electrode is properly formed before pressing.
- Pressing Equipment: Pressing equipment is used to compress the silicon electrodes to the required thickness and density. This step is crucial for improving the mechanical properties of the anode and ensuring that the electrode has the necessary structural integrity.
- Plasma Treatment Equipment: Plasma treatment is often used in the final stages of anode production to modify the surface properties of silicon particles or coatings. Plasma treatment can improve the bonding between silicon and the binder, enhancing the electrode's overall performance.
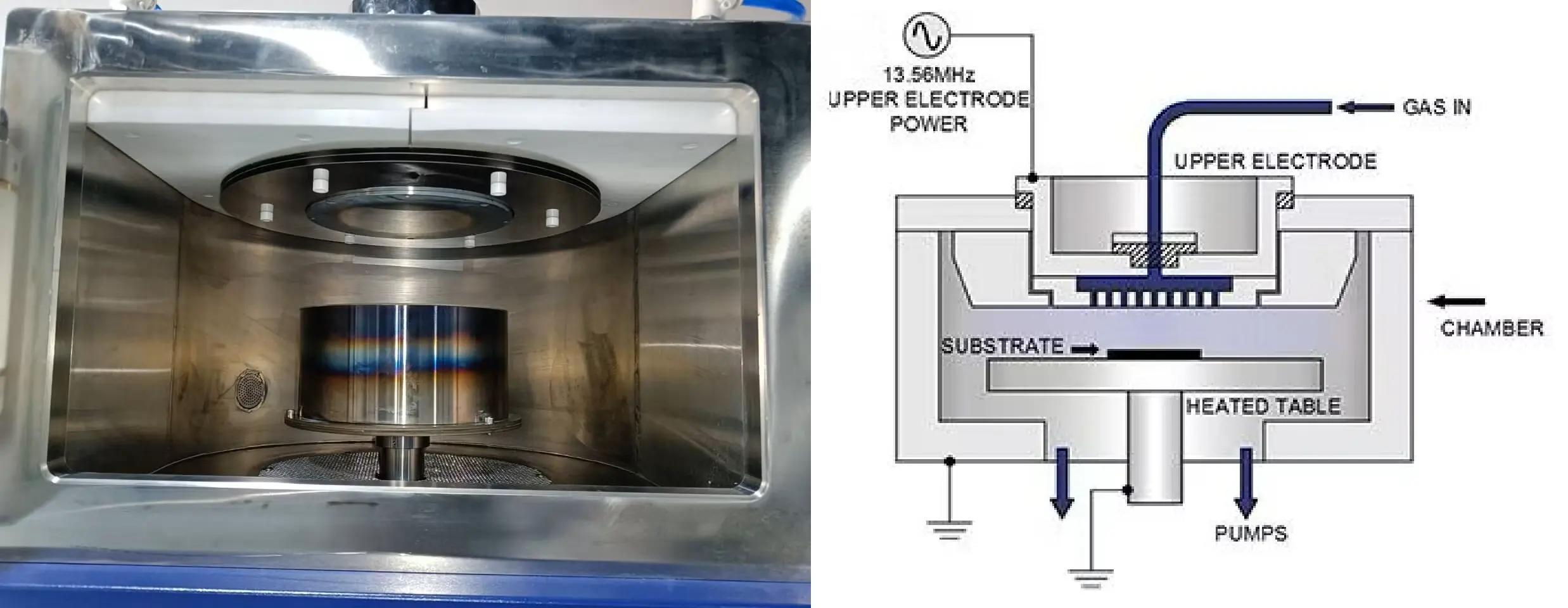
4. Challenges in Scaling-Up Silicon Anode Production
While the potential for silicon-based anodes is high, several challenges must be addressed to scale up production effectively.
Volumetric Expansion
One of the primary challenges of silicon anodes is the significant expansion (up to 300%) during lithiation and contraction of silicon during charge and discharge cycles. This expansion can cause mechanical stress, leading to electrode degradation and capacity loss. Scaling up production involves developing scalable solutions to mitigate this issue, such as incorporating advanced composites or protective coatings.
Material Stability
The instability of silicon anodes, especially in pure form, remains a challenge. Silicon anodes can suffer from poor electrochemical stability, leading to capacity fading and reduced cycle life. The formation of solid electrolyte interfaces (SEI) and silicon-electrolyte interactions can degrade the anode material over time. Scaling production requires the development of stable composite materials that can withstand long-term cycling.
Cost of Production
Silicon anode materials are generally more expensive than graphite-based materials, primarily due to the complexity of production processes and raw material costs. The cost of raw materials can significantly impact the overall production cost. Scaling up production requires the development of cost-effective methods, such as improving manufacturing efficiency by using advanced manufacturing techniques, and sourcing lower-cost raw materials by optimising the supply chain.
Reproducibility and Quality Control
The production process involves multiple steps, each requiring specialised equipment and precise control. Ensuring consistency and quality across large-scale production can be challenging. Achieving uniformity in the particle size, morphology, and structure of silicon particles is crucial for ensuring consistent performance across battery cells. As production volumes increase, maintaining high-quality standards and consistent product characteristics becomes more difficult.
Environmental and Sustainability Concerns
The environmental impact of silicon anode production, particularly in terms of energy consumption and waste generation, is an important challenge for scaling up. Efforts must be made to develop more sustainable production processes to reduce environmental footprints.
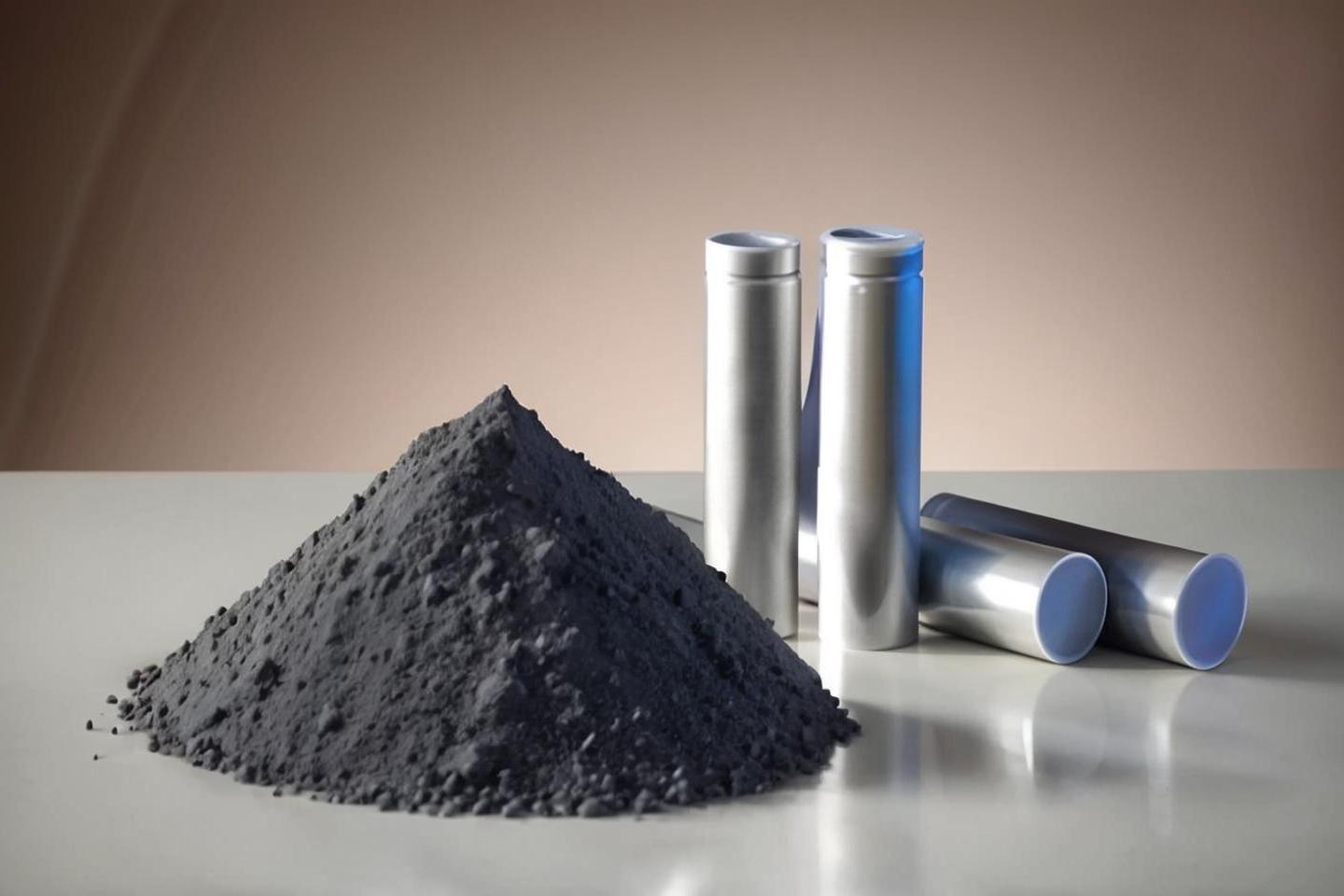
5. Impact of Several Key Technologies
5.1 Electrochemistry: Electrochemical behaviour plays a critical role in the performance of silicon anodes. Silicon undergoes significant volume changes during charge-discharge cycles, which can cause mechanical failure of the anode. Advances in electrochemistry, such as the development of advanced electrolyte formulations and better electrode design, are crucial for improving cycle life and stability. The electrochemical performance of the anode is highly dependent on the interaction between the silicon particles and the surrounding electrolyte, and innovations in this area are needed for scaling up production.
5.2 Thin Film: Thin film technology is widely used in silicon anode production to create highly uniform coatings of silicon or silicon-based materials on substrates. Thin films can improve the performance of silicon anodes by reducing the distance between the active material and the current collector, enhancing conductivity, and improving structural stability during cycling. Thin films are also used to apply protective coatings to the silicon to reduce volume expansion and prevent degradation.
5.3 Plasma Coating: Plasma coating is a promising technique for improving the surface properties of silicon anodes. Plasma treatment can enhance the bonding of silicon to the binder, promote uniformity in the coating, and reduce surface defects. Plasma coating can also be used to deposit thin protective layers, such as silicon oxide or carbon, which help mitigate the expansion and contraction of silicon during cycling.
6. Conclusion
The production of silicon anodes involves several complex stages, from material refinement to electrode formation, using specialised equipment such as ball mills, CVD reactors, and coating machines. Scaling up production of silicon anodes presents several challenges, including material instability, cost, and the impact of volume changes during cycling. Advances in electrochemistry, thin-film technology, and plasma coating play a crucial role in addressing these challenges, enabling the development of more stable and efficient silicon anodes. With scaling-up the production of silicon anodes, the future of high-performance batteries looks promising.
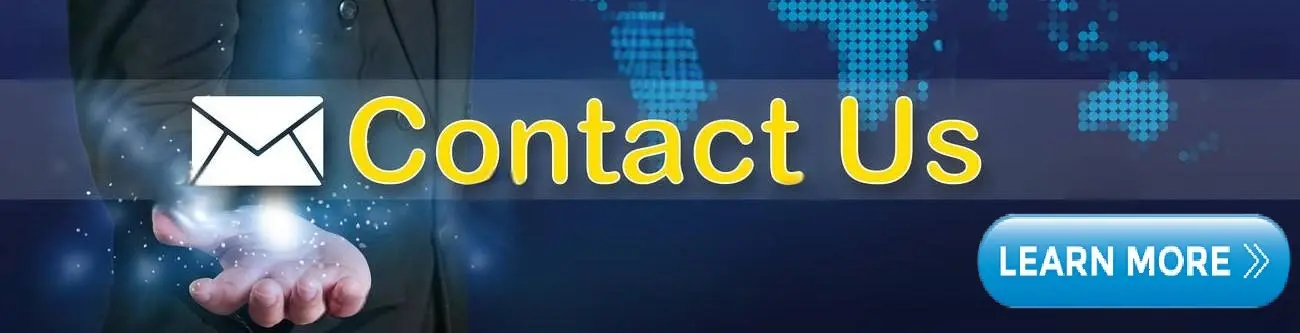
Back to the list