Electrical Equipment in the Petrochemical Industry: Safety, Maintenance, and Troubleshooting
1. Introduction
The petrochemical business is a complex and highly regulated industry that heavily relies on electric motors, generators, and drives for various operations. These electrical components are essential for processes such as pumping, compressing, and generating power within petrochemical plants. However, the hazardous environments present in petrochemical facilities necessitate stringent safety measures, meticulous maintenance, and strict regulatory compliance for electrical equipment. Their proper functioning and safety are of utmost importance due to the hazardous nature of the petrochemical environment.
2. Safety of Electrical Equipment Products
Hazardous Environments
Petrochemical plants often contain flammable gases, vapours, and combustible dust. Electrical equipment used in such areas must be designed and rated to prevent ignition sources. Electrical equipment used in potentially explosive atmospheres must be certified for use in such environments. For example, explosion-proof motors and drives are required in zones where flammable substances are present. These devices are constructed with enclosures that can withstand and contain an internal explosion without allowing flames or hot gases to escape and ignite the surrounding flammable gases or vapours.

The IEC System for Certification to Standards Relating to Equipment for Use in Explosive Atmospheres (IECEx) is a widely recognised certification scheme. In the European Union, the ATEX directive serves a similar purpose, ensuring equipment meets necessary safety requirements for potentially explosive atmospheres. Most common classes of the motors for explosion protection types Exeb, Exec, Exd (low voltage only), and Exp used in petrochemical, oil and gas industry.
Protection Mechanisms
Electrical equipment is equipped with multiple safety features. Petrochemical facilities often operate in extreme conditions. Motors and generators must be able to function reliably in temperatures ranging from -50°C in cold regions to +55°C in hot climates. While considering the factors preventing malfunction under extreme cold weather, proper cooling systems, such as IC411, IC511, and IC611 classified by IEC, or equivalent codes defined by NEMA, are crucial for maintaining equipment performance and longevity in hot temperature.
Ground fault protection is crucial as it detects leakage currents and quickly shuts down the equipment to prevent electric shock and potential fire hazards. Overload protection safeguards motors from excessive current draw, which can lead to overheating and damage. Temperature sensors are also incorporated to monitor the internal temperature of motors and drives. If the temperature exceeds a safe limit, the equipment can be automatically shut down or an alarm can be triggered to alert operators.
3. Maintenance Plans
Routine Inspections
Regular visual inspections of electrical equipment are the first line of defence. Technicians should check for any signs of physical damage, such as cracks in enclosures, loose connections, or frayed wires. They should also inspect cooling systems, ensuring that fans are operating properly and air vents are not blocked. Lubrication levels of motor bearings should be checked and topped up as needed.
Routine Testing
Periodic electrical testing is necessary to assess the performance of motors and drives. This includes insulation resistance testing to check the integrity of the electrical insulation. A decrease in insulation resistance can indicate potential breakdowns and the risk of short circuits. Motor current analysis can help detect imbalances or abnormal current patterns, which could signify problems such as misaligned shafts or worn bearings. Advanced analytics can then be used to predict when maintenance is required, optimising equipment performance and reducing downtime.
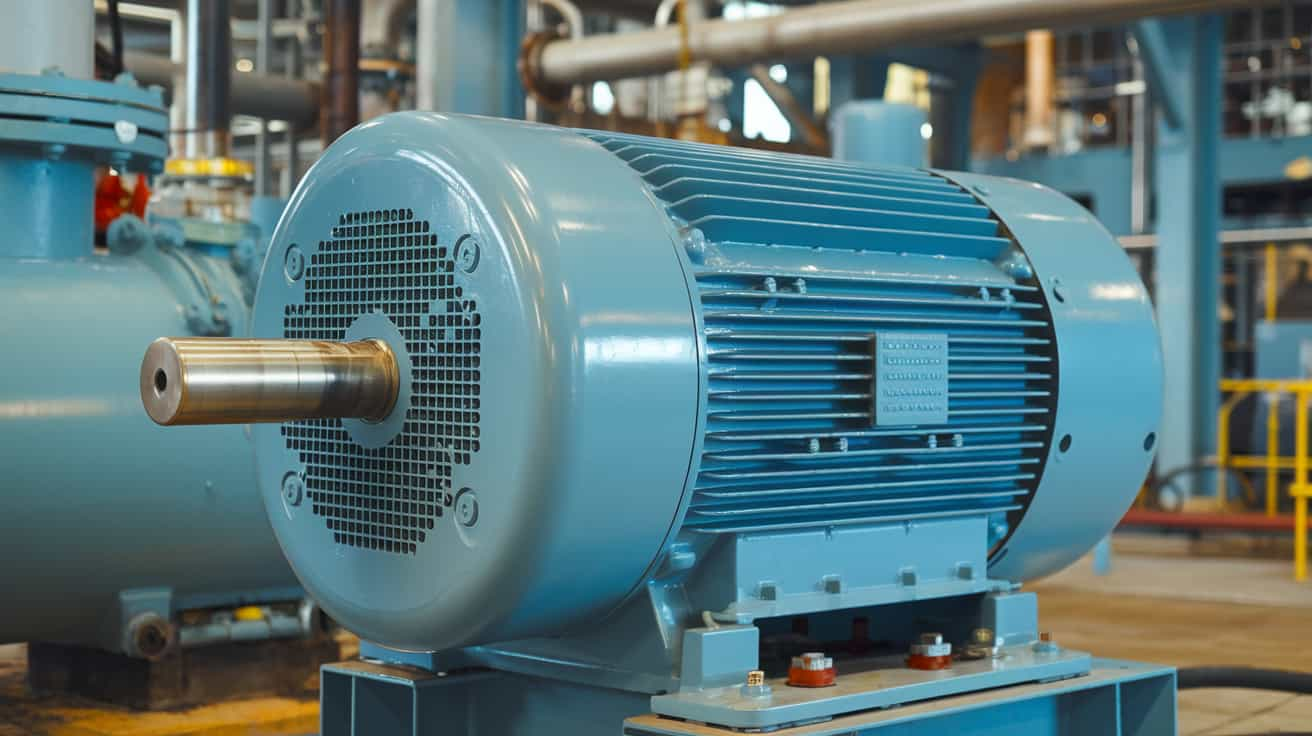
Component Replacement
Based on the results of inspections and testing, certain components may need to be replaced. For example, brushes in DC motors have a limited lifespan and need to be replaced when they are worn down. Capacitors in motor starting circuits may also degrade over time and require replacement to ensure proper starting and running of the motor.
Documentation and Keeping Record
Accurate documentation and traceability of all maintenance activities is vital. This includes records of inspections, test results, component replacements, and any repairs performed. These records help in tracking the history of the equipment, predicting future failures, and demonstrating compliance with regulatory requirements.
4. Regulatory Compliance
Industry Standards
The petrochemical industry adheres to various international and national standards. For global operations, the IEC standards specify requirements for electrical equipment used in hazardous areas. For example, IEC 60079 series covers electrical apparatus for explosive gas atmospheres, widely recognised and adopted worldwide. In the United States, compliance with OSHA 29 CFR 1910 (general industry) and 29 CFR 1926 (construction) is mandatory for electrical safety. The standards from NEMA, NEC, and API, provide guidelines for the installation and use of electrical systems in petrochemical plants. The big petrochemical company, such like Shell, PetroChina, Saudi Aramco, or Exxon Mobil Corp, etc. has their own company standards for electrical equipment procurement and internal production safety compliance. Compliance with these standards ensures that the equipment is designed, installed, and maintained in a manner that minimises risks.
Environmental Regulations
Petrochemical plants also need to comply with environmental regulations regarding the disposal of electrical equipment. Old motors and drives may contain hazardous substances such as lead, mercury, and PCBs. Proper disposal methods must be followed to prevent environmental contamination. Recycling programs are often implemented to recover valuable materials and reduce the environmental impact.
5. Troubleshooting Field Problems
Effective troubleshooting of electrical equipment in petrochemical facilities requires a systematic approach and a thorough understanding of the systems involved.
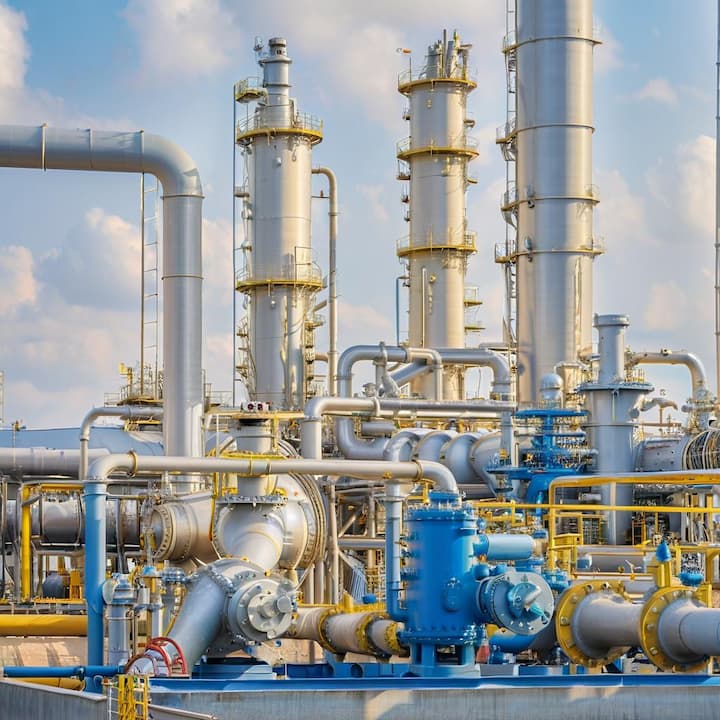
Common Problems and Solutions
- Motor Overheating: This could be due to excessive load, poor ventilation, or a faulty cooling system. Solutions may include reducing the load, cleaning the cooling fins, or replacing a defective fan.
- Vibration: Excessive vibration can be caused by unbalanced rotors, misaligned shafts, or worn bearings. Balancing the rotor, realigning the shaft, or replacing the bearings can correct the problem.
- Electrical Noise: Electrical noise can interfere with the proper operation of sensitive electronics in the plant. It may be caused by loose connections, damaged cables, or electromagnetic interference. Tightening connections, replacing damaged cables, and using shielding can help reduce electrical noise.
- Discontinuity: In the electrical system, the discontinuity is caused by loose wires, bad contacts, defective coils or coil leads, blown fuses, wires touching each other, or broken down insulation due to dirt or foreign objects. These problem can be found out and repaired during routine maintenance with visual inspection and checking with instrument such like multimeter, etc.
Systematic Approach
When an electrical equipment failure occurs, a systematic approach to fault diagnosis is required. Technicians should follow a practical, systematic to troubleshooting typically involves the following steps:
- Observe the system and establish what it does or does not do to gather information about the symptoms,
- Review current schematic diagrams and understand the circuit operation,
- Use troubleshooting reference charts provided in OEM maintenance manuals,
- Check continuity and voltage levels in the circuit by using tools like multimeters to measure electrical parameters such as voltage, current, and resistance,
- Apply the halving principle to localise the faults
- Consider substitution of easily replaced components
- Consult troubleshooting records of past difficulties and solutions, or subject matter expert for advices.
6. Conclusion
In the petrochemical business, electric motors, generators, and drives play a vital role. Ensuring the safety of these electrical equipment products through proper design, protection mechanisms, and operating by well trained personnel is essential. This includes using properly certified equipment, implementing comprehensive maintenance plans, adhering to regulatory requirements, and employing effective troubleshooting techniques. By adhering to these principles and practices, petrochemical facilities can continuously improve their electrical safety practices and operational efficiency.
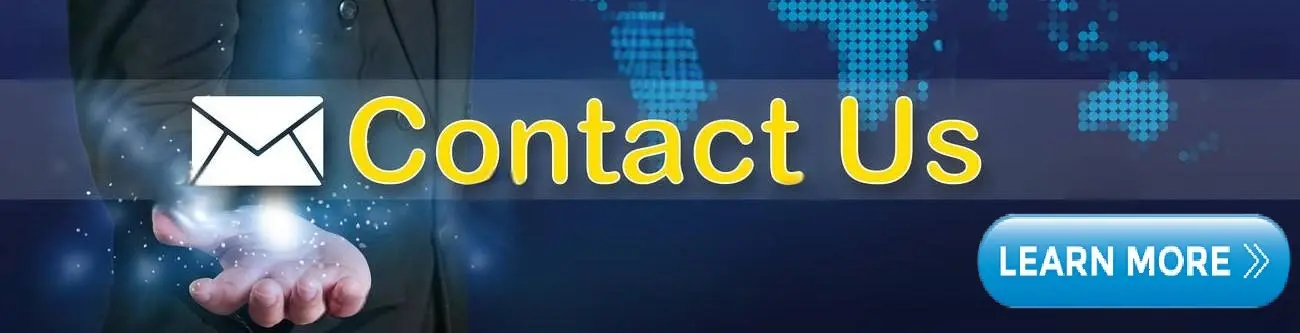
Back