Low Voltage Electric Motors: Keeping Machines Running in Nuclear Power Plants
Low voltage (LV) electric motors play a vital role in the operation of nuclear power plants (NPPs), where reliability and safety are paramount. These motors drive essential equipment from cooling, ventilation to auxiliary and utility systems, such as pumps, fans, blowers, and other machinery. Any failure could impact plant safety or availability. To ensure optimal and safe performance, it is essential to follow specific technical recommendations and establish a robust installation and maintenance plan of LV electric motors in large-scale gigawatt NPPs as well as SMR power plant.
Range and Selection:
In a typical GigaWatt nuclear power plant, between 400 and 800 LV motors are installed to support various critical and auxiliary systems. The exact number can vary depending on the plant design, the type of nuclear reactor (e.g., Pressurised Water Reactor (PWR), European Pressurised Reactor (EPR), or others), and specific operational requirements. The voltage of the LV motors is from 380V to 690V AC. The common voltage of those is 460V/480V in USA NPPs or 400V/415V in European NPPs. The power range of the motors is vary. For example, the small LV motors are 2.2 ~15 kW used in auxiliary systems, chemical injection, and monitoring equipment. The medium motors are 15 ~ 75 kW commonly found in cooling systems, HVAC, and water treatment. The large LV motors are 75 ~ 400 kW used in safety systems and critical cooling applications such like low/high pressure safety injection pumps.
It’s crucial to choose motors that are appropriately sized for the load requirements to avoid overheating and premature failure. When selecting the LV motors, the following points shall be taken into consideration.
- Motor Efficiency and Reliability: Select motors designed for high efficiency and reliability to minimise energy consumption and reduce the risk of failure, minimum IE3 efficiency. The motors shall also comply with industry standards like NEMA, IEC, and AFCEN's RCC-M and RCC-E codes.
- Seismic Qualification: In nuclear environments, the motors must withstand seismic events. Ensure that motors are seismically qualified according to the required plant standards, such as IEEE 344 or RCC-E.
- Environmental Conditions: The motors should be designed to operate in harsh environments with high radiation, temperature fluctuations, and humidity, i.e. special insulation and protection measures should be implemented to prevent degradation over time. Use motors with appropriate enclosure types (e.g., IP55, IP65) to protect against dust, moisture, and other contaminants.
- Monitoring: The motors should include provisions for vibration sensors to monitor performance and detect early signs of mechanical issues like misalignment or bearing wear.
- Protections:
- Overload Protection: The motors should be equipped with thermal overload relays to prevent damage from excessive current during abnormal operating conditions.
- Ground Fault Protection: Implementing ground fault relays to detect insulation failures, which can lead to short circuits.
- Redundancy: For critical applications, consider motor redundancy, allowing backup motors to take over in the event of primary motor failure.
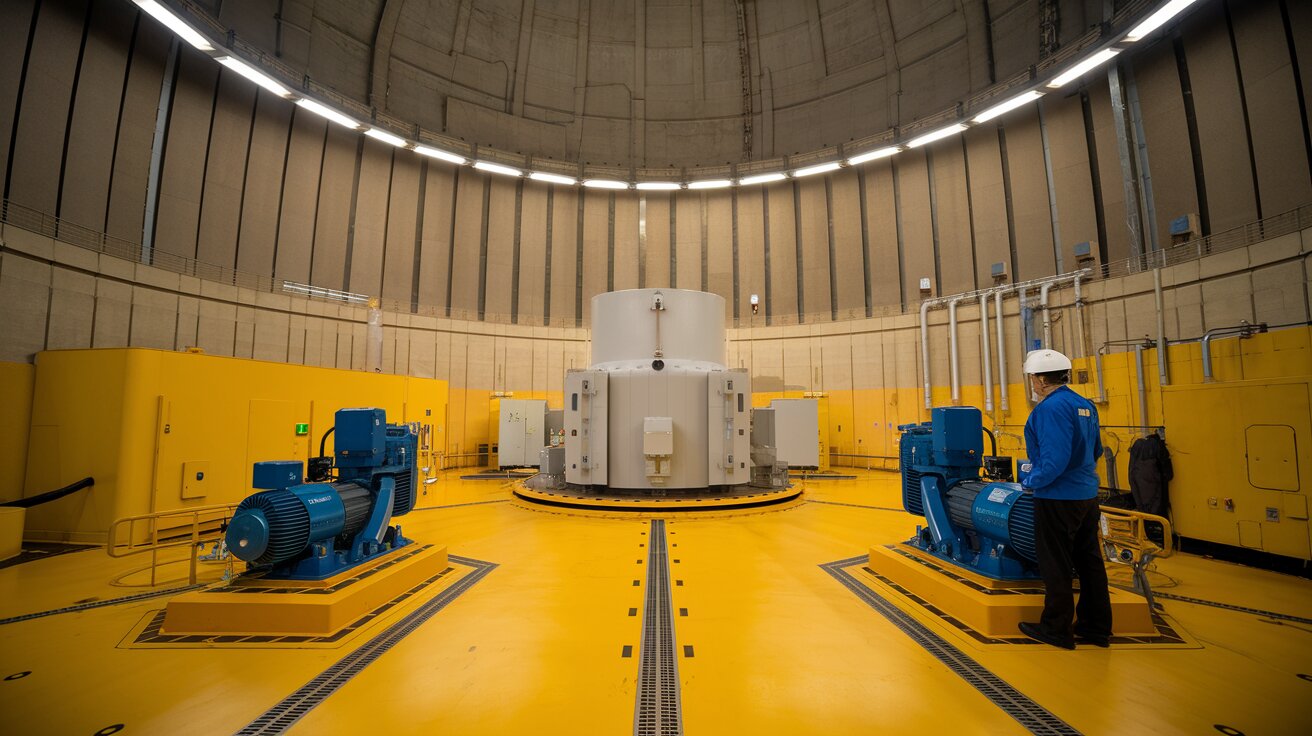
Installation
- Operating condition:
The installation area must be properly ventilated to prevent dust accumulation on the motors surface. The LV motors should be protected from direct radiation exposure when possible inside the nuclear island, except those at special requirements with specified dose. For the motors installed outdoor, the operating temperature and humidity ranges should be double checked with the site condition. - Mounting and alignment:
Use rigid mounting bases with vibration isolation pads. The motors shall be properly mounted to the driven equipment to reduce vibration and ensure smooth operation. Use precision alignment tools to align the motor shaft with the driven equipment shaft, reducing wear and tear on bearings and couplings. - Electrical connections:
- Implement cable management systems with radiation-resistant materials. Use appropriate cable sizes and types to minimise voltage drop and ensure proper motor performance.
- Install surge protection devices to safeguard the motor from voltage spikes and transients.
- Grounding and bonding:
- Ensure proper grounding of the motors to prevent electrical shock and protect against electrical faults
- Implement bonding practices to minimise electrical interference and ensure safety.
Maintenance
Preventive Maintenance:
The scheduled inspections will be carried out periodically checking for signs of wear and tear, such as bearing noise, increased vibration levels, and overheating. The visual inspections should focus on cable insulation, connections, and motor housing integrity. The motor bearings should be lubricated at regular intervals based on manufacturer recommendations to reduce friction and extend motor lifespan. The electrical testing should be routinely performed such as insulation resistance testing, dielectric absorption ratio testing, and polarisation index testing to assess motor winding health and insulation quality.
Predictive Maintenance:
Use advanced techniques like vibration analysis, thermal imaging, and motor current signature analysis to predict motor failures before they occur. The sensors and data log will track and analyse data trends over time to detect early signs of wear, degradation, or performance issues.
Safety Considerations
The major safety concern is to implement ALARP principles during installation and maintenance. For example, use appropriate PPE during inspections, monitor cumulative radiation exposure, and minimise time in high-radiation areas. It’s important to schedule maintenance programme during planned outages for increasing productivity and cost reduction.
Conclusion
The installation and maintenance of LV electric motors in nuclear power plants require careful consideration of technical recommendations and a comprehensive maintenance plan. By selecting the right motors, ensuring proper installation, and implementing a robust maintenance program, the plant operators can enhance the reliability, efficiency, and safety of their electric motor asset. Proper installation and maintenance not only extend equipment life but also contribute to overall plant safety and efficiency. Regular preventive maintenance, condition monitoring, and timely repairs for the LV motors are essential to minimise downtime, reduce operating costs, and ensure the continuous and safe operation of the nuclear power plants. They will generate reliable, clean electricity and heat for several decades!
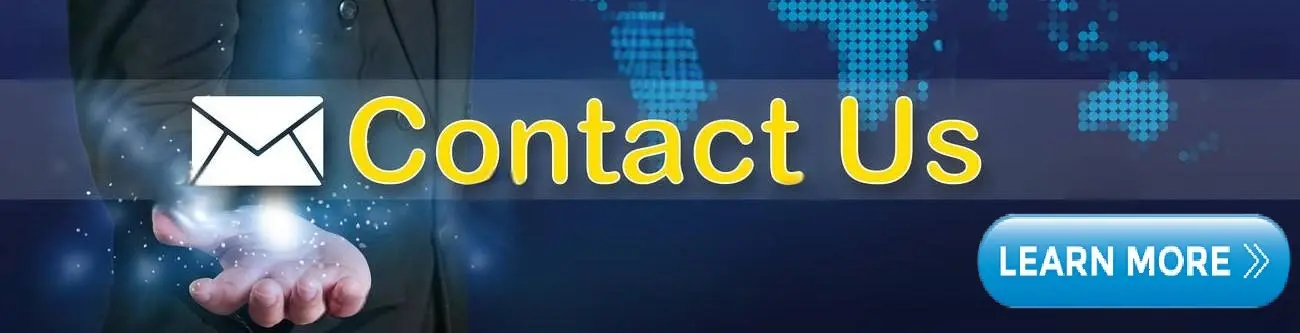
Back